Concrete Delivery: Ready Mix VS Volumetric
It’s no secret that we at skEYEwatch have a strong interest in the concrete production industry. Our team specializes in creating technologies such as concrete dispatch software, GPS tracking software, truck camera systems and more! With this being said, let’s explore the differences between ready mix vs volumetric trucks. Both of these are incredibly useful within the concrete production industry, though each has its own unique pros and cons. Keep reading below to learn more!
Key Differences: Ready Mix VS Volumtric
Before we dive in, keep in mind that these are general differences and the specific circumstances of a construction job, such as the job site conditions, volume of concrete required, and logistical considerations, may influence which type of truck is more suitable.
![]() |
![]() |
|
---|---|---|
Mixing Method | Concrete is mixed at a central plant and transported in a rotating drum. | Concrete is mixed on-site in the truck using an auger. |
Flexibility | Limited to the specific batch mixed at the plant. | Can produce different mix designs on demand. |
Wastage | Unused concrete can go to waste. | Reduced waste as concrete is mixed on demand. |
Timing | Concrete must be used before it sets, requiring precise timing. | Not a concern as concrete is mixed immediately before use. |
Quality Control | Concrete is mixed under controlled conditions at a plant, leading to consistent quality. | Quality depends on operator's skill and on-site conditions. Can be adjusted on the spot. |
Concrete Discharge | Concrete is kept in the rotating drum and discharged through a chute. The speed of the drum's rotation controls the rate of discharge. | Concrete is mixed by the auger and then moved towards the chute for delivery. The auger's speed controls the rate of discharge. |
Washout Process | Washout is required after delivery to avoid hardened concrete in the drum. This requires a designated washout area and may create environmental concerns. | Typically easier and quicker as the auger and mixing chamber can be flushed out on-site. This also tends to be less wasteful and more environmentally friendly as unused materials can be saved for future use. |
Ready Mix Concrete Trucks
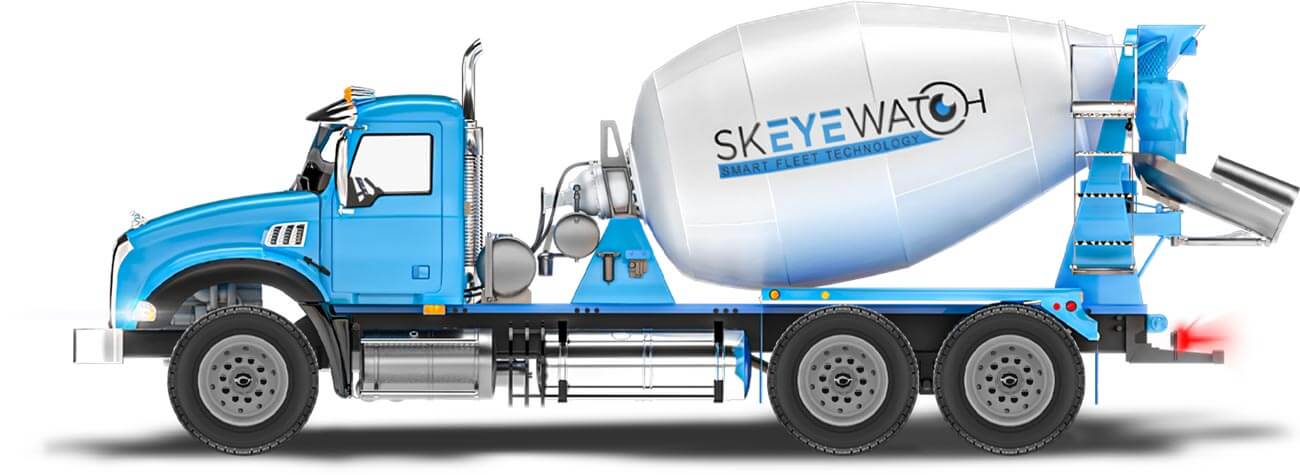
Now let’s let’s talk more about ready mix trucks. These trucks transport pre-mixed concrete from a central batch plant to the job site. The concrete is mixed at the plant, loaded into the drum of the truck, and then kept in motion until it is time for it to be poured. This method requires precise planning and timing, as the concrete must be used before it hardens. This type of concrete truck allows for efficient, cost-effective delivery of large amounts of concrete without having to spend time mixing it on site.
Without ready mix trucks, large-scale construction projects would not be possible due to the difficulty in transporting ready mix concrete over long distances and in difficult terrain. As such, ready mix trucks are an important component of the modern construction industry.
Who manufactures Ready Mix Trucks?
This question can be broken down into 2 parts, the “truck” manufacturer and the “mixer” manufacturer.
Ready Mix "Truck" Manufacturers
First, there’s the truck manufacturers that build and assemble the truck’s chassis, cab, engine and drivetrain. This would include the whole truck without the mixer attached. These manufacturers also build the truck bases for other specialized heavy duty trucks (aka lorries) such as dump trucks, garbage trucks, roll off trucks and more! After this phase of the vehicle production, the truck will roll off the production line and head over to the mixer manufacturer. Just below is a list of popular U.S. based truck manufacturers that create the vehicles for ready mix industry.
- Autocar
- Freightliner (Daimler Truck)
- International (Navistar, Inc)
- Kenworth (Paccar Inc)
- Mack (Volvo)
- Oshkosh S-Series
- Peterbilt (Paccar Inc)
- Terex Advance
- Volvo
- Western Star (Daimler Truck)
Ready Mix Truck "Mixer" Manufacturers
The second phase of ready mix truck production is the mixer. These are the manufacturers of the large spinning barrels and machinery that is attached to these purpose built trucks. The mixer includes the frame assembly, barrel, hopper and all technology that helps regulate the spinning barrels and the charging and discharging of the wet concrete. This also includes the hydraulic cylinders that are added for controlling tipping and the riser arms that allow for ready mix concrete to discharge from the drum.
The ready mix concrete is then loaded into a hopper so it can be fed into an onboard mixing drum. The mixing drum is attached to a drivetrain consisting of a gearbox, transmission and engine which powers the rotation of the drum. This ensures that ready mix concrete is properly mixed before being discharged out of the ready mix truck. Here’s a list of a some ready mix concrete truck “mixer” manufacturers commonly used in the U.S.
- Autocar
- Beck
- Continental (CBMW)
- Con-Tech Manufacturing
- London
- Revolution Mixers (formally McNeilus)
Scenarios Where Ready Mix Trucks Might Be More Useful:
- Large Volumes: For large projects where a high volume of concrete is needed at once, ready mix trucks can be more efficient as they can carry a large batch of pre-mixed concrete.
- Strict Quality Control: For projects where consistent quality is crucial, ready mix concrete may be preferred. It is mixed under controlled conditions at a plant.
- Short Delivery Times: If the job site is near the batching plant and the concrete can be poured immediately upon arrival, ready mix trucks can deliver the concrete efficiently.
- Standardized Mix Design: If a project only requires a standard type of concrete, a ready mix truck can deliver this without the need for on-site adjustments.
- Efficient for Repeat Jobs: For construction jobs where the same specific mix is needed repeatedly, ready mix trucks can be more efficient as the concrete is pre-mixed at the plant.
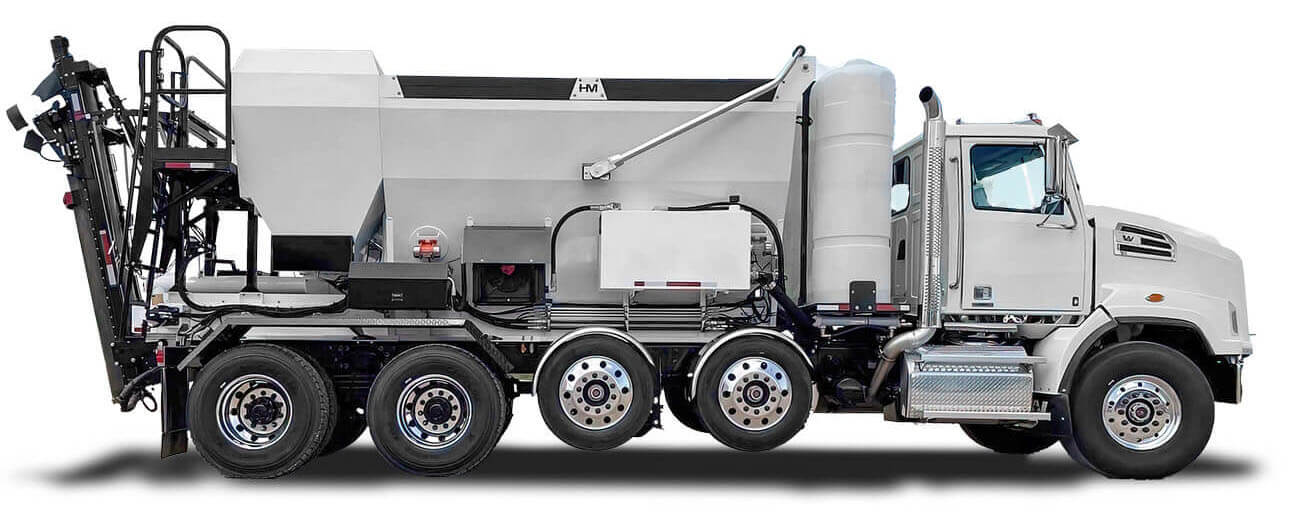
Volumetric Concrete Trucks | Metered concrete trucks
Now let’s dive into volumetric trucks. These trucks are essentially mobile concrete plants. They carry the separate ingredients for concrete (sand, cement, water, and other admixtures) in separate compartments and mix them on-site as needed. This allows the operator to adjust the mix design and volume on the fly, providing flexibility in terms of quantity and type of concrete produced.
Volumetric trucks use an auger for mixing the concrete. The auger mixes the cement, sand, water, and any other admixtures together to produce concrete. After the mixing process, the auger also helps to move the concrete towards the chute for delivery.
The advantage of this approach is that it allows for greater control and customization of each batch since all of the measurements can be adjusted onsite according to specifications or changes required by the conditions of the project. Additionally, this method also allows for smaller batches to be made which can be extremely helpful when working with tight spaces or limited access points where bringing in a ready mix truck might not be possible or practical.
Volumetric Concrete "Truck" Manufacturers
Just like ready mix trucks, volumetric concrete trucks start with a foundation consisting of the entire truck minus the mixer. It wouldn’t be uncommon to see these truck manufacturers with a volumetric mixer attached.
- Freightliner (Daimler Truck)
- International (Navistar, Inc)
- Kenworth (Paccar Inc)
- Mack (Volvo)
- Peterbilt (Paccar Inc)
- Volvo
- Western Star (Daimler Truck)
Volumetric Truck "Mixer" Manufacturers
The second production phase of volumetric concrete trucks are the mixers. Below is a list of several different manufacturers of onsite / on demand mixing machines that are permanently attached to the rear of these trucks.
Volumetric Concrete Production: How it works...
Mobile mixing concrete trucks (volumetric trucks) are revolutionizing how we do construction projects. Instead of hauling ready-made batches from a factory, these innovative vehicles make it possible to whip up the perfect blend onsite – with each batch containing precisely mixed ingredients like sand, gravel, cement and water for optimal results. The rear mixers feature storage compartments so that every measurement is exact down to the last grain of sand!
When an order is placed and ready to start production, the truck operator can easily dial in the mix design with one click. With precision accuracy of +/-1 percent for every pour due to dual auger cement metering technology, sand and stone pass through their own gate before falling precisely into the mixing auger that meters out exactly the needed amount of cement – easy as pie!
The precise concrete mix is then carried to the discharge chute where it is ready to pour on the job site with practically no waste.
Scenarios Where Volumetric Trucks Might Be More Useful:
- Variable Demand: If the exact amount of concrete needed is uncertain, a volumetric truck can be a good choice. It can mix the precise amount required on site, reducing wastage.
- Different Mix Designs: If a project requires different types of concrete mix, a volumetric truck can easily adjust the mix design on the spot.
- Remote Locations: For projects in remote locations where a ready mix plant is far away, a volumetric truck can be useful as it can produce fresh concrete on-site.
- Longer Delivery Times: If there are potential delays on the job site or long travel times, a volumetric truck can be advantageous. Since the concrete is mixed on-site, there’s no risk of the concrete setting in the truck before it can be used.
- Small Quantities: For smaller projects where a full truckload from a ready mix plant may be too much, a volumetric truck can mix just the right amount.
In conclusion, both concrete trucks have their unique purposes
Overall, both methods are useful for different circumstances and both provide effective solutions for getting concrete to the job sites and completing projects efficiently. However, when dealing with larger projects or tight budgets it may be better to use a ready mix truck while smaller jobs may benefit more from the flexibility and customization offered by a volumetric truck.
Smart Fleet Technology for the concrete Industry
Thanks for reading our blog post about ready mix vs volumetric concrete production. If you have investment interest into concrete or construction materials industry, then we highly recommend that you check out our product offerings at skEYEwatch. Below is a list of some of our most popular applications that our customers are already using in the concrete industry.
FAQs
FAQs About Ready Mix & Volumetric
Common answers to common questions about ready mix vs volumetric.
What is the difference between ready mix concrete and volumetric concrete delivery?
How does volumetric concrete delivery save time when compared to ready mix concrete?
How much more expensive is volumetric concrete delivery compared to ready mix?
What advantages does volumetric mixing provide over regular ready mix?
What are some advantages of using ready mix concrete?
Does volumetric blending produce a higher quality product than ready mix?
Yes! Volumetric blending provides better consistency than pre-mixed solutions due its ability produce a variety of blends according exact requirements laid out by engineers or architects before beginning work onsite - making it easier for contractors to adhere strictly specified levels regarding ratios between components such as water/cement ratios or air content measurements which are considered essential elements used in determining durability of structures created utilizing these types of mixes when compared against those made using regular pre-mixed bags found at most hardware stores.
How accurate are measurements used when creating ready mix concrete?
Update Notice:
This blog post was updated on June 6th, 2024 to fix broken links and ensure all information is current. We strive to provide you with the most accurate and useful content. If you have any questions or notice any issues, please feel free to contact us.
Recent Developments:
Rebranding: McNeilus Mixers has rebranded to Revolution Concrete Mixers™ following an acquisition by Right Lane Industries. The rebranding includes a new logo and website, and the corporate headquarters has relocated to Rochester, Minnesota. Read the full announcement Revolution Concrete Mixers.
Oshkosh S-Series Trucks: Oshkosh has moved details about their S-Series trucks to a new dedicated website, which can be accessed Oshkosh S-Series Front Discharge Mixers.
Peterbilt Update: We have updated the link to the Peterbilt website. Their latest Vocational truck model has changed from the 365 series to the 567 series. You can find more information Peterbilt Truck Model 567.